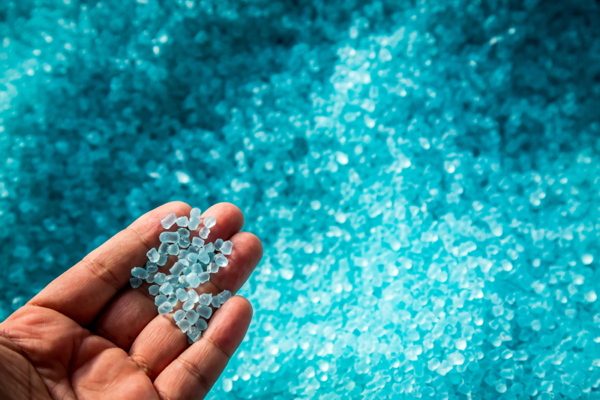
Face au défi du siècle visant à réduire la consommation mondiale de plastiques et mieux gérer la fin de vie des emballages, les solutions de recyclage gagnent en popularité et l’Union Européenne a d’ailleurs fixé des objectifs ambitieux imposant des packagings composés à 50% de plastique recyclé d’ici 2025. Mais tributaires d’infrastructures de collecte plus ou moins matures selon les pays et de technologies de recyclage thermomécanique peu souples, les recycleurs peinent à répondre en quantité aux demandes de plastiques actuellement.
« On vise des flux de déchets qui n’existent pas. Aujourd’hui, il manque 1 million de tonnes par an de collecte pour remplir ces objectifs », assure Martin Stephan, directeur général adjoint de la société Carbios, une société de bioplasturgie basée à Clermont-Ferrand pionnière du recyclage chimique. « L’Union européenne estime qu’il manque 4 milliards d’euros d’investissements nécessaires en Europe pour atteindre les objectifs de 2025 ».
La technologie thermomécanique implique de broyer et de fondre certains types de plastiques, en général les plus courants, mais non colorés. Ce procédé a aujourd’hui le mérite d’augmenter la durée de vie du plastique, mais se heurte à une grosse contrainte de limite des ressources pour un résultat qualitatif inférieur au matériau vierge.
« Le recyclage mécanique a ses limites car il ne permet pas de recycler indéfiniment un même emballage, le plastique perd peu à peu ses propriétés mécaniques. De plus, il y a beaucoup de produits contaminants que l’on ne peut éliminer », explique un fabricant.
Faire du neuf avec du vieux
Face à l’enjeu que représente l’approvisionnement en rPET (PET recyclé), startups et industriels de la plasturgie travaillent d’ores et déjà à une nouvelle génération de recyclage sur la base d’un procédé chimique de dépolymérisation puis repolymérisation du PET. Au contraire du procédé mécanique, cette technologie possède l’énorme avantage de revenir après le processus de recyclage à une résine totalement vierge.
« À partir de 100% de déchets, cette technologie va pouvoir générer un volume beaucoup plus intéressant et avec une qualité identique au vierge », indique Gilles Swyngedauw, directeur innovation et RSE chez Albéa, qui vient de signer le New Plastics Economy Global Commitment de la Fondation Ellen MacArthur s’engageant ainsi sur un principe d’économie circulaire.
Les marques se mobilisent et passent déjà commande auprès des futurs fournisseurs de ce nouvel or vert. L’Oréal et L’Occitane ont ainsi signé des accords de partenariat avec le canadien Loop Industries, un des pionniers de la technologie du recyclage chimique.
En France, la société Carbios est en phase d’industrialisation d’une solution prometteuse à partir d’un procédé de transformation enzymatique. « Grâce à une enzyme spécifique au PET, nous cassons la chaine de molécules du plastique. Notre procédé va déconstruire ce polymère pour revenir aux deux monomères d’origine. Il suffit ensuite de les repolymériser pour refaire une matière identique à un PET vierge », explique M. Stephan. La technologie fournira aux pétrochimistes le moyen de produire du PET « vierge » non plus seulement à partir de pétrole mais à partir de déchets, y compris les vêtements polyester ou les plastiques colorés, et ce, à l’infini. Les premières productions devraient apparaître en 2023/24. « Ce n’est pas de la réutilisation, c’est vraiment du recyclage », ajoute M. Stephan.
Spéculations et incertitudes
Pour les fabricants d’emballages, premiers confrontés aux contraintes d’approvisionnement, la perspective du recyclage chimique représente assurément l’opportunité d’une ressource additionnelle, plus qualitative. Néanmoins, plusieurs s’interrogent sur ce nouveau modèle.
De fait, en apportant leur soutien financier, au travers de pré-réservations de volumes, aux fournisseurs de rPET en phase de recherche et développement sur ces technologies, les marques imposent pour l’avenir un choix de fournisseur unique à leurs partenaires fabricants d’emballage.
« Nous sommes assez surpris de ce modèle où les transformateurs sont écartés de la démarche. Dans la chaîne de valeur traditionnelle, il y a le fournisseur de matière première qui fournit le transformateur qui fournit le client final. Demain, les matières premières seront imposées par les marques et cela risque d’avoir une influence assez forte sur la chaine de la valeur complète. Les fabricants ne seront plus maitres de leurs achats et la responsabilité en cas de problème de fabrication sera éclatée. Il peut y avoir un danger dans ce type d’approche », assure Vincent Joffre, directeur commercial de PRP Création.
Pour l’heure, ces annonces de rapprochement offrent aux marques une résonnance médiatique évidente tout en suscitant l’émulation autour de cette technologie tant attendue.